Nissan Sentra Service Manual: Replacement operations
Description
This section is prepared for technicians who have attained a high level of
skill and experience in repairing collision-
damaged vehicles and also use modern service tools and equipment. Persons
unfamiliar with body
repair techniques should not attempt to repair collision-damaged vehicles by
using this section.
Technicians are also encouraged to read Body Repair Manual (Fundamentals) in
order to ensure that the original
functions and quality of the vehicle can be maintained. The Body Repair Manual
(Fundamentals) contains
additional information, including cautions and warning, that are not including
in this manual. Technicians
should refer to both manuals to ensure proper repairs.
Please note that these information are prepared for worldwide usage, and as
such, certain procedures might
not apply in some regions or countries.
The symbols used in this section for cutting and welding/brazing operations
are shown below.
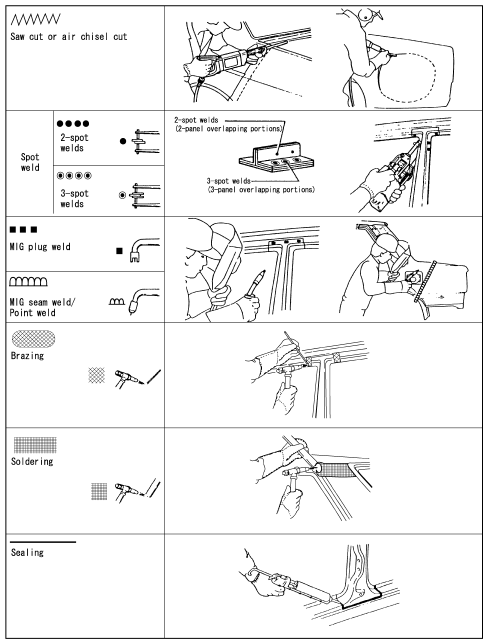
- Front pillar butt joint can be determined anywhere within shaded
area as shown in the figure. The best location for the butt joint is at
position A due to the construction of the vehicle. Refer to the front
pillar section.
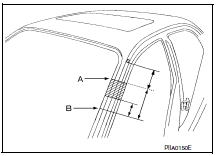
- Determine cutting position and record distance from the locating
indent. Use this distance when cutting the service part. Cut outer
front pillar over 60 mm above inner front pillar cut position.
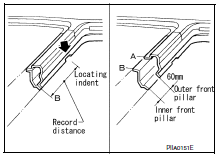
- Prepare a cutting jig to make outer pillar easier to cut. Also, this
will
permit service part to be accurately cut at joint position.
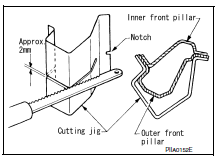
- An example of cutting operation using a cutting jig is as follows.
- Mark cutting lines.
- Cut position of outer pillar
- Cut position of inner pillar
- Align cutting line with notch on jig. Clamp jig to pillar.
- Cut outer pillar along groove of jig. (At position A)
- Remove jig and cut remaining portions.
- Cut inner pillar at position B in same manner.
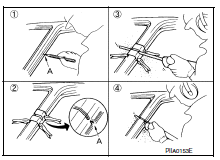
Hoodledge
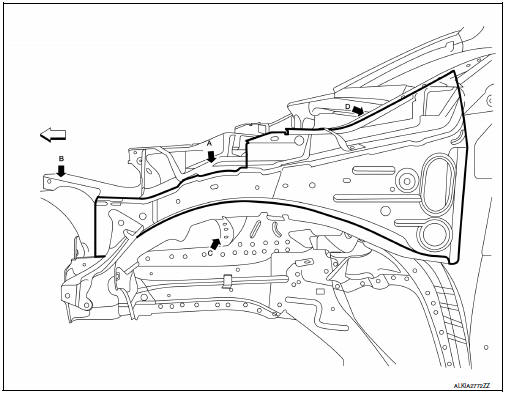
Change parts
- Front hoodledge
- Radiator core support upper
- Front strut housing (LH)
- Hoodledge connector
Front
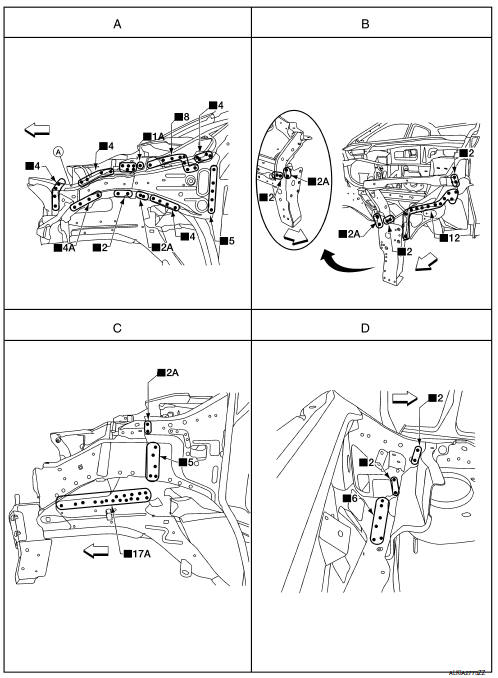
Front Side Member
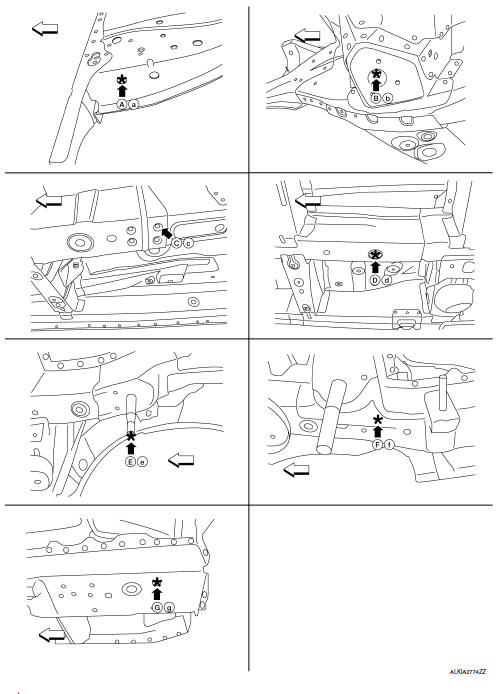
Change parts
- Front side member front assembly
Front Pillar
OUTER
- Work after hoodledge and hoodledge reinforcement rear has been removed.
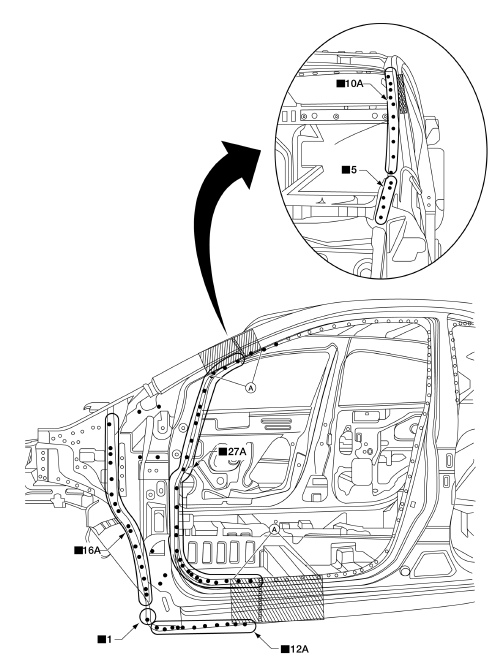
- Front pillar section of body side outer
- Recommended sectioning location
REINFORCEMENT
- Work after front pillar outer has been removed.
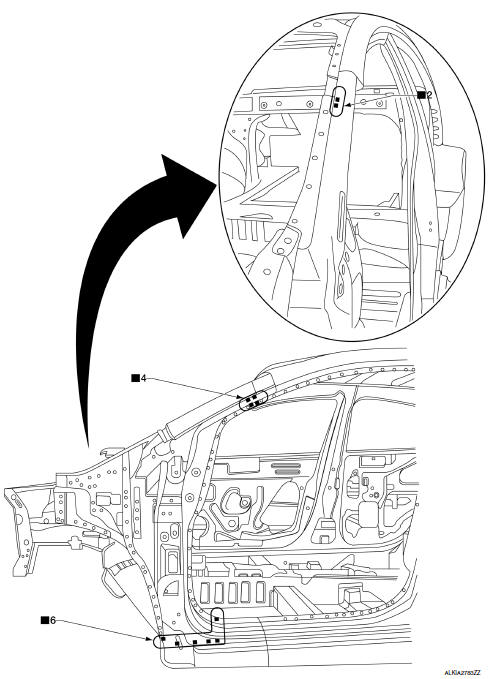
- Front pillar reinforcement
INNER
- Work after front pillar reinforcement has been removed.
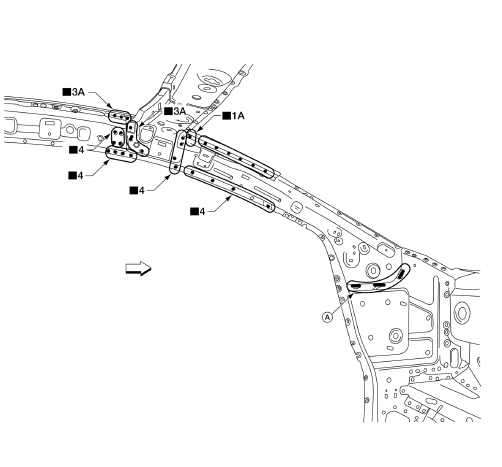
- Front pillar inner reinforcement
- Stitch mig welds
Dash Side
Work with front pillar reinforcement removed.
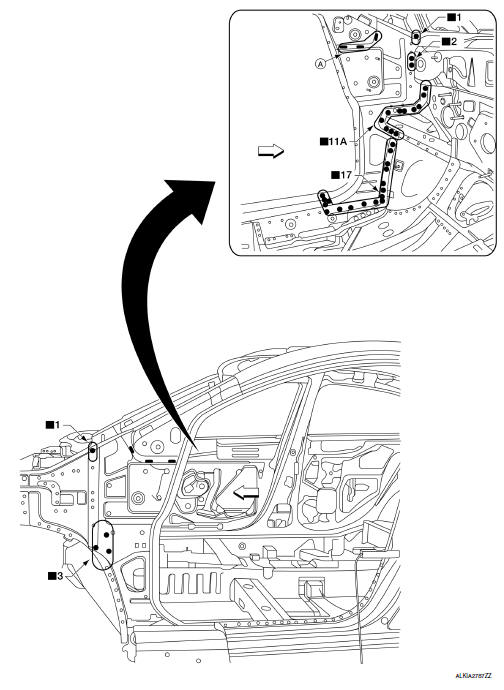
- Stitch mig weld
Center Pillar
OUTER
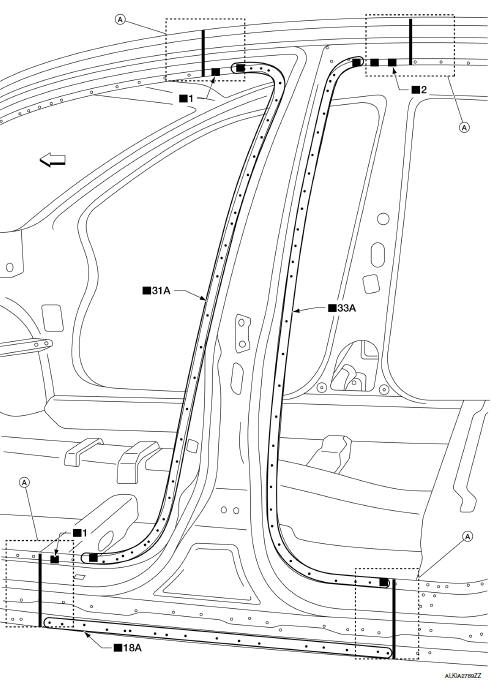
Change parts
- Center pillar portion of body side outer
recommended sectioning area.

- 165 mm (6.5 in)
- 140 mm (5.5 in)
- 45 mm (1.8 in)
Removal
- Use a cut off wheel to make pre-measured cut in upper center
pillar outer body side.
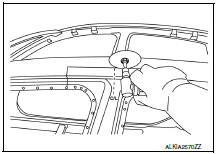
- Cut the sill area (A) between the sill plate holes (B) on the lower
center pillar outer body side.
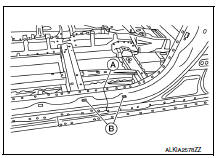
- Drill spot welds that attach the center pillar outer body side. Only
drill through the outer panel.
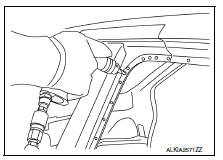
- Remove the center pillar outer body side.

Installation
Match welds locations from removed part onto new panel and weld into place.
REINFORCEMENT
Work after center pillar outer has been removed.
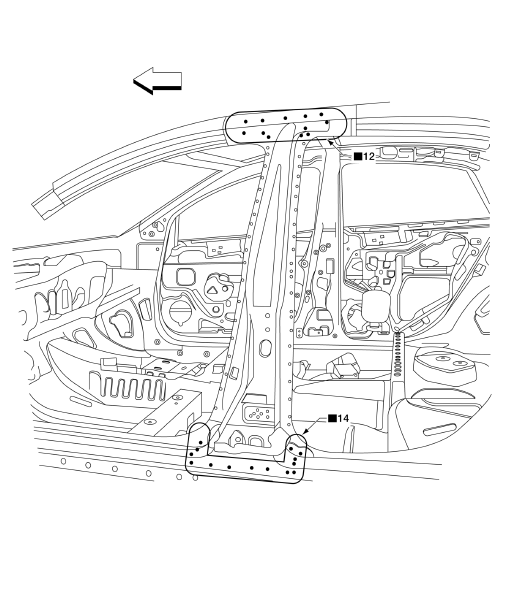
- Center pillar reinforcement
Front
Roof
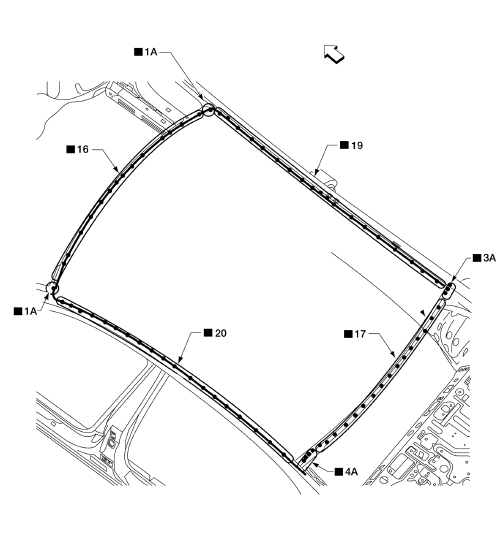
Front
REMOVAL
- Remove the headlining. Refer to INT-40, "Removal and Installation".
- Remove the roof side moldings (RH/LH). Refer to EXT-32, "Removal and
Installation".
- Remove the windshield glass. Refer to GW-12, "Removal and Installation".
- Remove the rear window glass. Refer to GW-26, "Removal and
Installation".
- Drill out spot welds using a 8.0 mm (0.31 in) spot weld removing bit (A)
on the windshield and rear window
glass flanges.
NOTE:
Only drill through the first layer of metal (the roof outer panel)
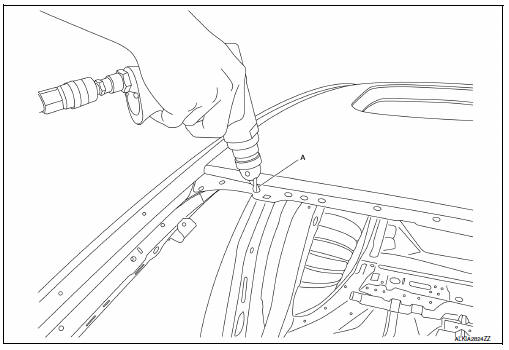
- Use an angle head grinder and a 3.18 mm (0.125 in) cutting wheel (A) to
grind through the first layer only.
NOTE:
Only grind through the first layer of metal (the roof outer panel)
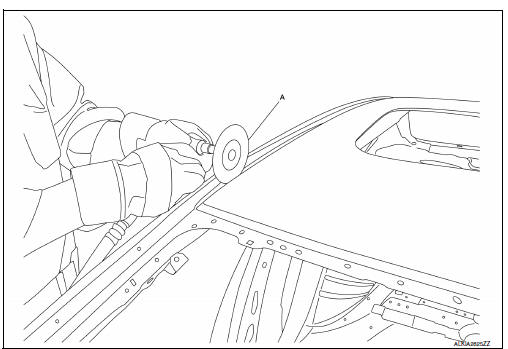
- Remove roof panel (1).
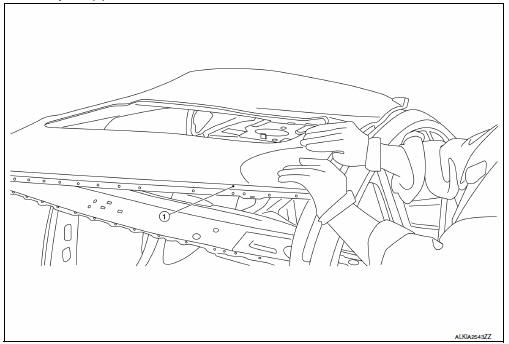
PREPARATION
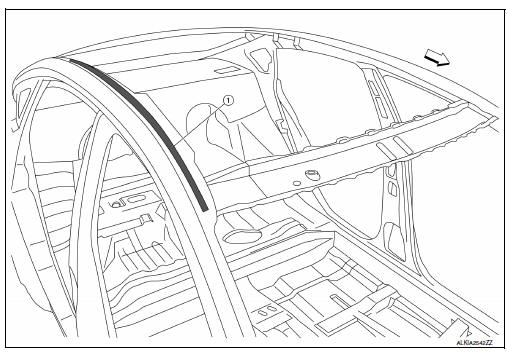
- Weld through primer
Front
- Grind all mating surfaces around the roof flanges.
- Test panel for proper alignment and fit.
- Remove panel.
- Compare to the removed panel, then drill 8.0 mm (0.31 in) holes in the
same location on the new roof
panel.
- Use 3M weld through primer to prime body side upper and the front and
rear window flanges
INSTALLATION
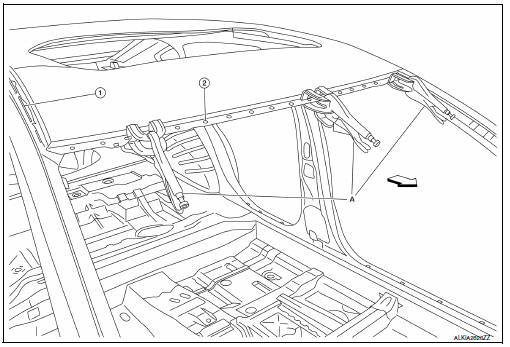
- Body side upper spot welds
- Plug welds
- Clamping pliers
Front
- Check the dimensions and fit.
- Use clamping pliers to retain the roof panel to the front and rear
window flanges.
- Plug weld as necessary.
- Dress welds as necessary to allow proper glass fit.
- Refer to NISSAN approved panel refinishing
- Install the headlining. Refer to INT-40, "Removal and Installation".
- Install rear window glass. Refer to GW-26, "Removal and Installation".
- Install windshield glass. Refer to GW-12, "Removal and Installation".
- Install roof side moldings (RH/LH). Refer to EXT-32, "Removal and
Installation".
Outer Sill
Work after the front pillar reinforcement, center pillar reinforcement, and
rear fender have been removed.
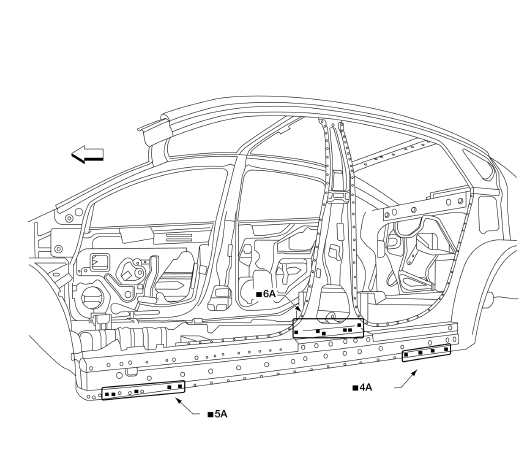
Front
Rear Fender
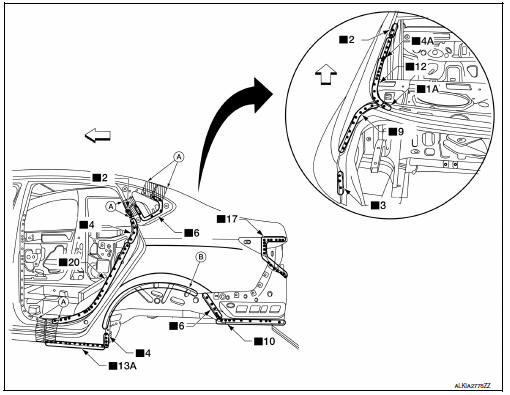
- Recommended cut zone
- Bonded hem flange
Front
Rear Panel
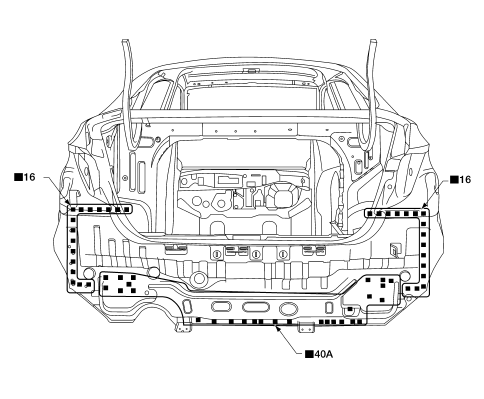
Rear Floor Rear
- Work after rear panel assembly has been removed.
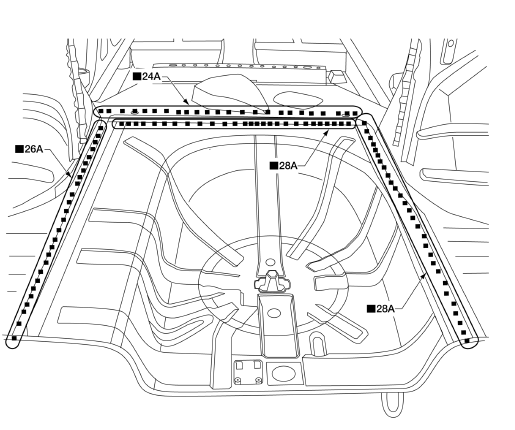
Rear Side Member Extension
- Work after rear panel assembly and rear floor rear have been removed.
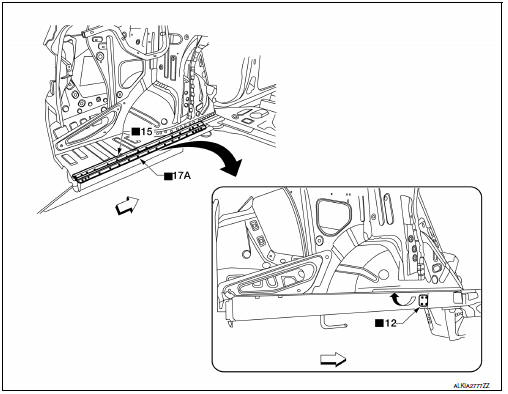
- Rear side member extension
Front
Description
The following figure shows the areas which are sealed at the factory. Sealant
which has been applied to these
areas should be smooth and free from cuts or gaps. Care should be taken no ...
Other materials:
CVT Fluid filter
Exploded View
Transaxle assembly
CVT fluid filter
Fluid filter cover
CVT fluid
Removal and Installation
REMOVAL
Remove neighboring parts of CVT fluid filter.
Remove fluid filter cover mounting bolt (A).
Remove fluid filter cover (1) from transaxle by rotating leftw ...
Rear disc brake
Brake Burnishing
CAUTION:
Burnish contact surfaces between brake pads and disc rotor
according to the following procedure
after refinishing the disc rotor, replacing brake pads or if a soft pedal
occurs at very low mileage.
Be careful of vehicle speed. Brakes do not operate firmly/sec ...
Ecu diagnosis information
Audio unit
Reference value
TERMINAL LAYOUT
PHYSICAL VALUES
Bose speaker amp
Reference value
TERMINAL LAYOUT
PHYSICAL VALUES
BluetoothВ® control unit
Reference value
TERMINAL LAYOUT
PHYSICAL VALUES
...
© 2014-2025 Copyright www.nisentra.com